Technologies
We excel in a wide range of technologies, making us a leader in our industry. Our offerings cover the entire value chain in the production of ceramic products and components. Additionally, we manufacture our own advanced forming tools as well as a wide variety of specialised processing machines, often incorporating a high degree of automation.
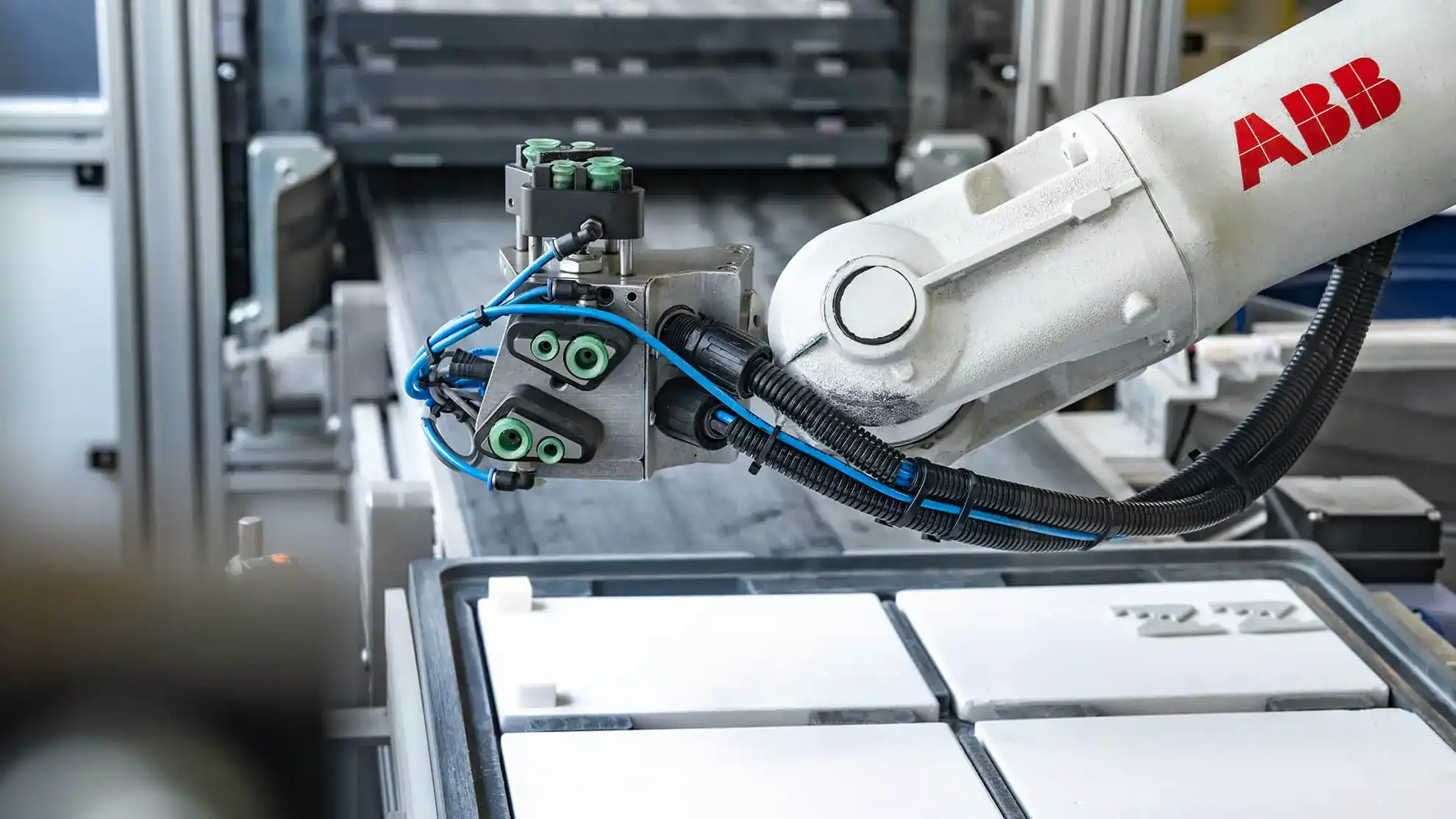
Shaping methods
Process in detail
Our production facilities master all shaping processes for technical ceramics. This allows us to offer our customers everything from the production of complex prototypes and challenging small series to large-scale production with attractive cost structures.
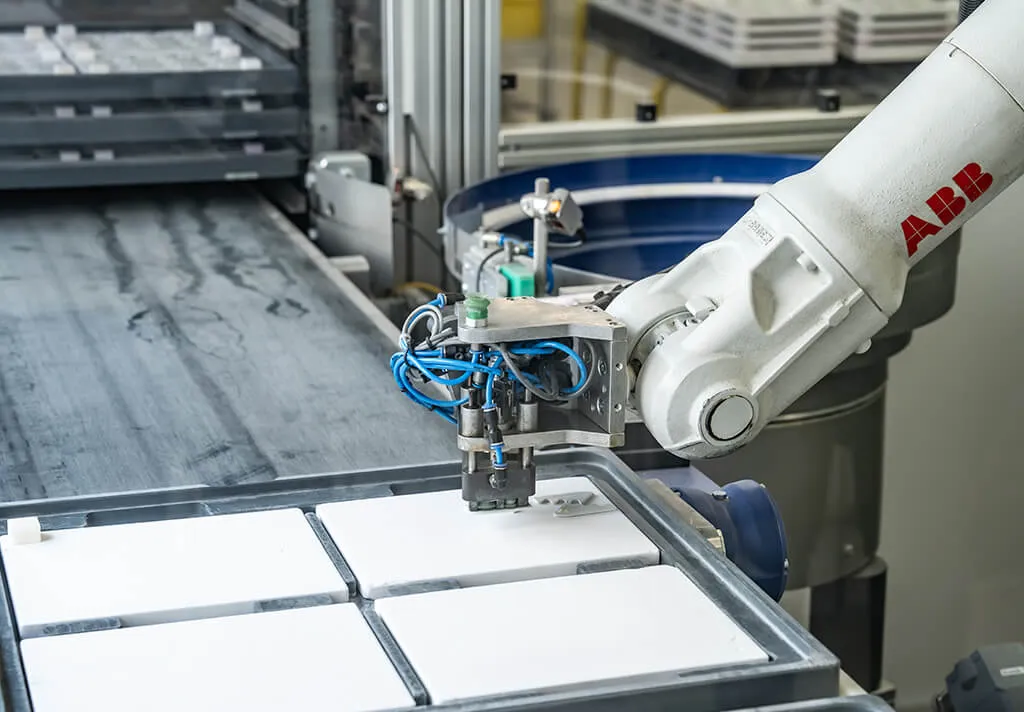
Injection Moulding
Degrees of freedom in shaping
Similar to plastics, ceramic moulded parts can also be produced using the injection moulding process. This method offers additional degrees of freedom in shaping, especially for freeform surfaces and intricate structures. Advanced tools such as core-spindle tools and vacuum technology are utilised. With over 20 injection moulding machines equipped with in-house developed automation systems, we can produce not only large quantities but also very complex component geometries. Overmoulding components is also part of our expertise.
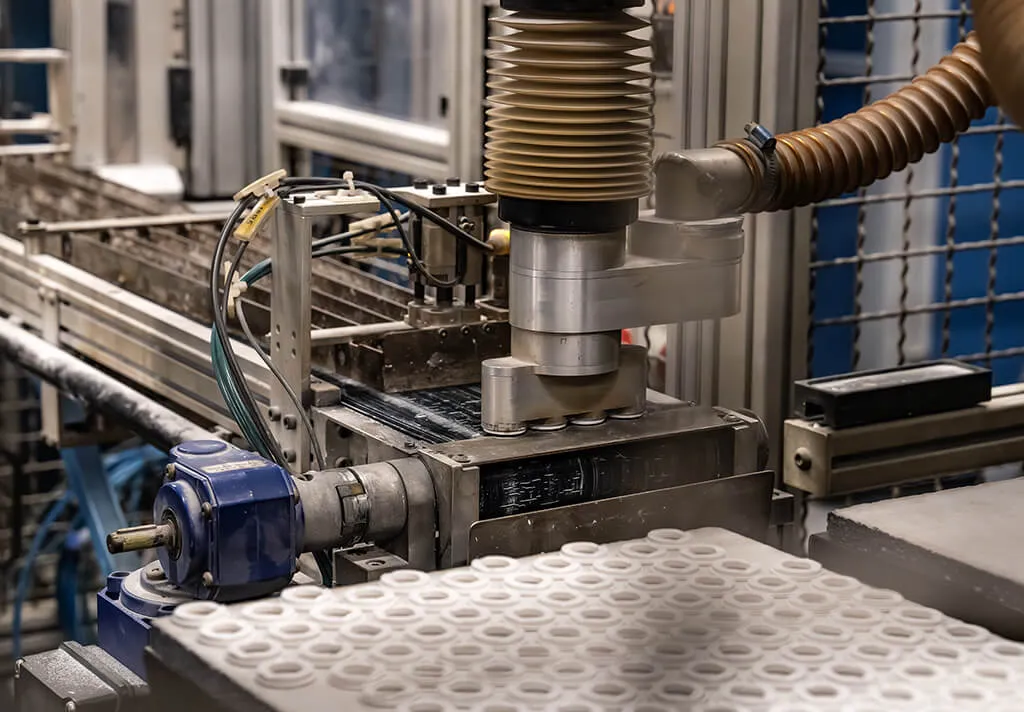
Uniaxial pressing
From 2 to 1600 tons
In this process, ceramic granulates are compacted into shaped parts using forming tools made of steel, hard metal, or ceramics.
- Production ranging from prototypes to large series
- Micro parts weighing less than approximately 0.2 g
- Large components weighing around 5 kg
- Up to 20 production cycles per minute
- Up to 30 shaped parts per cycle
With over 200 presses offering pressing forces from 2t to 1600t across five locations, Rauschert possesses one of the industry's most extensive manufacturing capacities.
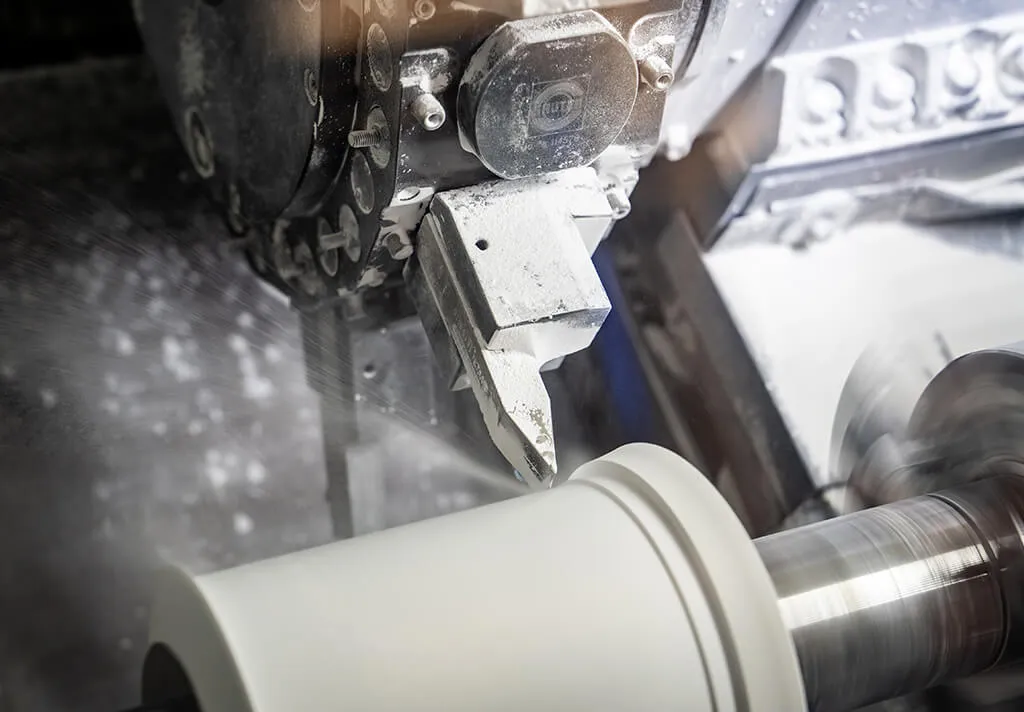
Green machining
Effort reduction after sintering
With high precision, we can quickly and cost-effectively adjust ceramic components toward their final geometry through machining processes (milling, turning) before sintering. Precision machining on the sintered part is then focused on fine-tuning and, in certain cases, can even be entirely eliminated. This enables us to save significant time and costs for our customers.
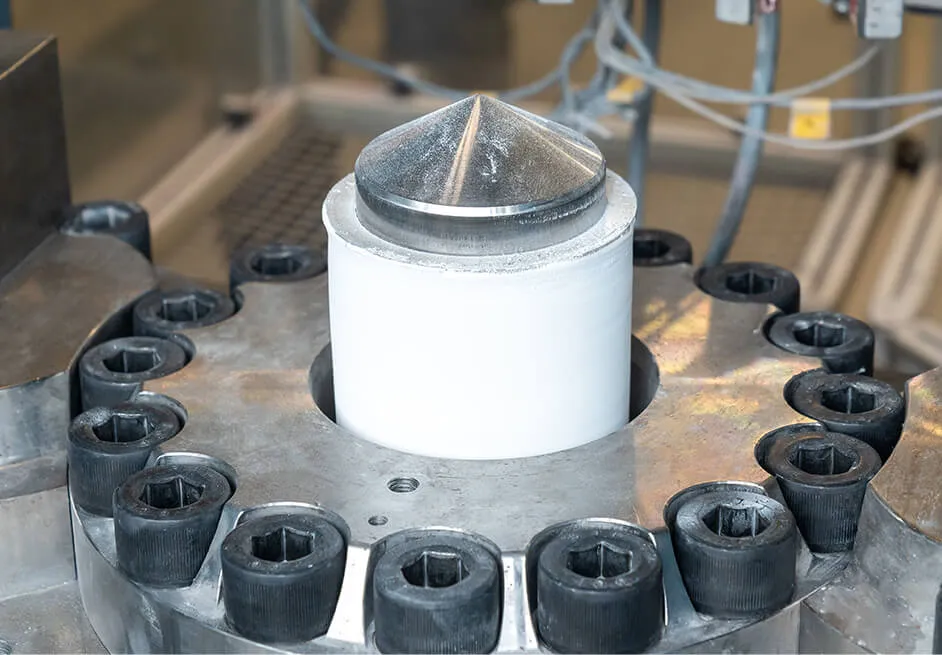
Isostatic pressing
Up to 4000 bar
Through the uniform compression of ceramic granulate from all sides with pressures of up to 4000 bar, components of exceptionally high quality can be produced. With multiple systems, we manufacture ceramic parts weighing up to 40 kg and with dimensions of up to a diameter of 500 mm and a height of 1500 mm.
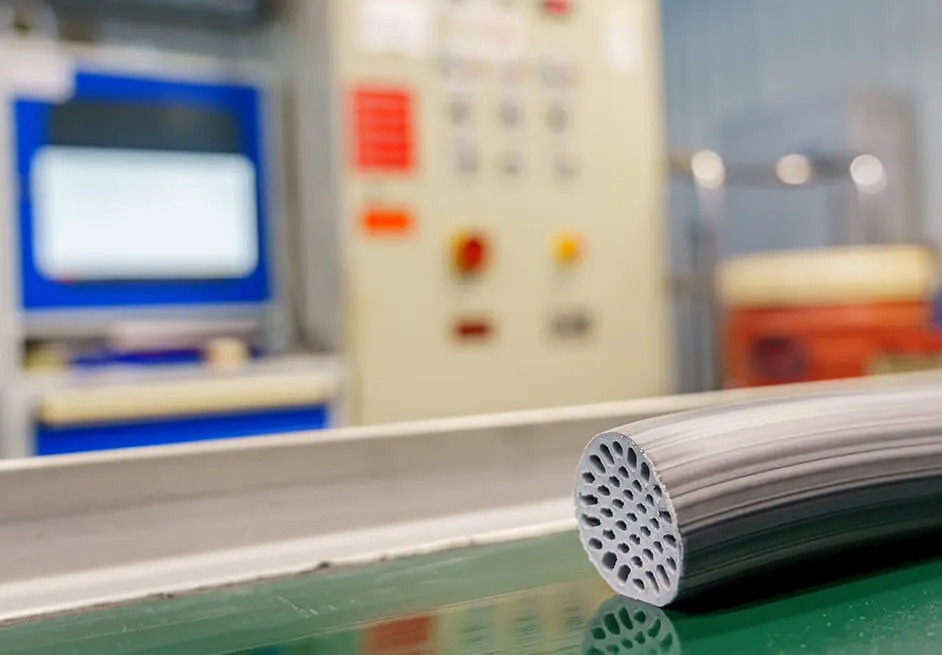
Extrusion
Wide variety of geometries
We efficiently produce rotationally symmetrical parts such as tubes, rods, and profiles in a wide variety of geometries. With more than 20 extrusion systems across five locations, we achieve part diameters ranging from 1 mm to 150 mm and lengths of up to 1200 mm. We specialise in intricate structures with very small diameters, multi-hole tubes with numerous openings, and ceramic honeycomb bodies with up to 600 cpsi.
Casting
Traditional manufacturing process
By applying this traditional manufacturing process to modern high-performance ceramics, we can produce very complex and large components with limited setup effort, though it is restricted to smaller quantities. Using a model, we create plaster molds into which we pour specially prepared slips. After a drying period, the components can be demolded.
Additive manufacturing
Rapid prototyping
In collaboration with external partners, we offer prototyping using the lithography process. In agreement with RWTH Aachen, we are developing an innovative printing process using aqueous slips. This method uses the same ceramic materials as those in subsequent series production, enabling the creation of representative prototypes. We can produce the feedstocks ourselves cost-effectively, making additive manufacturing more economical even in industrial series production.
In addition to producing ceramic components, we also routinely use additive manufacturing for tool mould parts made of steel via the laser sintering process.